カジノミーカジノ
<ウェブサイト名>
<現在の時刻>
TOP ニュースリリースガイド ニュースリリースガイド一覧 新エネルギー 省エネルギー 材料 Focus NEDO FocusNEDO一覧 Focus NEDO第88号/特集 人とAIが協力し合う未来へ 次のAIが見えてきた Focus NEDO第87号/特集 省エネ・脱炭素への道をひらく 未利用熱エネルギー活用技術 Focus NEDO第86号/特集 AIエッジコンピューティング Focus NEDO第85号/特集 材料開発の革新に三位一体で挑む 超超プロジェクト 第84号/カーボンリサイクル・窒素循環・アンモニア発電・プラスチックリサイクル 資源循環社会への道 第83号/日本の主力エネルギーを目指す 再生可能エネルギー 第82号/イノベーション創出を加速 スタートアップ支援 第81号/実用化へのカウントダウン『セルロースナノファイバー』 第80号/イノベーションで未来をつくる NEDO40年のあゆみ 第79号/ムーンショット型研究開発事業-地球環境の再生へ Cool Earth & Clean Earth 第78号(技術戦略研究センター/スマートセル技術) 第77号(AI・ロボットのNEXTステージ/『オープンイノベーション白書』で読み解くイノベーション創出の今と未来) 実用化ドキュメント 実用化ドキュメント一覧 新エネルギー 省エネルギー 環境問題対策 電子・情報 材料 ロボット・AI・福祉機器 バイオ・医療 NEDO Channel NEDO Channel一覧 新エネルギー 環境問題対策 電子・情報 ロボット・AI・福祉機器 国際 分野横断 その他 NEDO Channel --> 検索 NEDO Channel NEDO公式X NEDO公式Facebook NEDOホームページ トップページ 実用化ドキュメント 驚異の新素材、 単層カーボンナノチューブ 世界初の量産工場が稼働 CONTENTS INTRODUCTION イントロダクション BEGINNING 極めて優れた新素材 量産化が課題 BREAKTHROUGH 産総研に送り込まれた 成否を分ける技術をもった人材 FOR THE FUTURE 量産化技術確立のためさらに人材を投入 FACE カーボンナノチューブの ポテンシャルの高さに魅せられた なるほど基礎知識 NEDOの役割 メニュー閉じる 材料 カーボンナノチューブキャパシタ開発プロジェクト 驚異の新素材、 単層カーボンナノチューブ 世界初の量産工場が稼働 日本ゼオン株式会社、国立研究開発法人産業技術総合研究所 取材:January, February 2016 INTRODUCTION 概要 2006〜2010年度に実施されたNEDOの「カーボンナノチューブキャパシタ開発プロジェクト」の下、日本ゼオン株式会社と国立研究開発法人産業技術総合研究所(以下、産総研)が、日本で初めて発見・構造解明された単層カーボンナノチューブの生産技術を確立しました。その結果、日本ゼオン株式会社は、単層カーボンナノチューブの量産工場を世界で初めて完成させ、2015年11月11日に稼働を開始しています。なお、この成果は功績を讃えられ、文部科学大臣表彰「科学技術賞」他を受賞しました。 BIGINNING 開発への道 極めて優れた新素材量産化が課題 カーボンナノチューブは日本で初めて発見された新素材です。1991年に飯島澄男さんが構造を解明しました。カーボンナノチューブはその名の通り、炭素原子同士が蜂の巣状に結合し、チューブ(筒)状になった構造をしています。直径は数ナノメートル(ナノは10億分の1)で、複数層のものを「多層カーボンナノチューブ」、1層のものを「単層カーボンナノチューブ」と呼んでいます〈図1〉。 なかでも単層カーボンナノチューブは、多層カーボンナノチューブに比べて、極めて高い性能を示しており、軽量でありながら、強度は鋼の20倍、熱伝導性は銅の10倍、電気伝導性は銅の1000倍と、極めて優れた素材としての注目を集めています。 この素材の活用に向け、世界各国で、その生産技術の研究開発が進められていましたが、なかなか量産化には至りませんでした。 このようななか実施されたのが、2006〜2010年度のNEDO「カーボンナノチューブキャパシタ開発プロジェクト」です。キャパシタとは電気を放出したり蓄えたりする、電子機器には欠かせない部品。カーボンナノチューブは高性能なキャパシタ開発を可能にします。さらに低炭素社会の実現に向け、複合部材製品の創出をはじめ、新材料として高いエネルギー利用効率・省エネルギー効果が期待されることから、国の大きな期待もかかっています。 このNEDOプロジェクトの下、日本ゼオンと産総研が共同で、単層カーボンナノチューブの生産技術の確立に取り組みました。 図1 単層カーボンナノチューブの分子構造(提供:産総研) 図2 NEDOの「カーボンナノチューブキャパシタ開発プロジェクト」で開発されたスーパーキャパシタ 約1000倍の生産効率、99.98%の高純度という画期的な合成法 ここで確立に取り組んだ単層カーボンナノチューブの生産技術は、2002〜2005年度に実施されたNEDOの「ナノカーボン応用製品創製プロジェクト」の成果が基になっています。その成果とは、産総研の畠賢治さんが2004年に開発した、単層カーボンナノチューブの画期的な合成法「スーパーグロース法(SG法)」という基盤技術です〈図3〉。 図3 スーパーグロース法のイメージ(提供:日本ゼオン) SG法は「化学気相成長(CVD)法」と呼ばれる合成法の一種で、最大の特徴は、単層カーボンナノチューブの生産効率と純度の高さにあります。従来の単層カーボンナノチューブの合成法に比べて、約1000倍の生産効率、99.98%の高純度で合成されます。そのため高速に大量合成することが可能で、1000分の1以下の生産コストを実現しているのです。こうした技術は他に例がなく、世界中の研究者が強い関心を寄せています。 「ナノカーボン応用製品創製プロジェクト」への畠さんの参画の経緯を、産総研の湯村守雄さんはこう説明します。 「私は当時、産総研でカーボンナノチューブの合成法を研究しており、カーボンナノチューブの発見者である飯島澄男さんを産総研に招へいしました。飯島さんをプロジェクトリーダーとして、このNEDOプロジェクトが始まりました。その矢先、アメリカで、CVD法によりカーボンナノチューブを合成する技術を学んできた畠さんが帰国したというので、NEDOプロジェクトのメンバーの一員として参画するようにお願いしたのです」 畠さんは留学先のハーバード大学で、カーボンナノチューブの合成法の一種であるCVD法を勉強していました。「しかしCVD法は合成収率が非常に低く、実用化には程遠いレベルでした。そこで、NEDOプロジェクトで、CVD法の合成収率の向上に取り組むことにしたのです」と畠さん。 収率とは、ある化学プロセスにおいて理論上得られるはずの物質量に対する実際に得られた物質量の割合のことです。一般にこれが高いほど、そのプロセスが優秀で実用化に向くことを意味します。 「触媒を失活すると考えられていた、触媒を覆う炭素の殻を除去するために、ごく微量の水分を合成雰囲気に添加しました。その結果は予想を超える驚くべきものでした。これまでの製法に⽐べて、合成収率は約1000倍に達したのです。収率が2倍になれば、大成功と思っていたので、ここまで効果があるとは想像もしていませんでした」と畠さんは振り返ります。 2004年2月に畠さんは、この製法をSG法と名付け、同年8月にフラーレン・ナノチューブ・グラフェン学会で発表。さらに同年11月にはサイエンス誌に掲載され、国内外で大きな反響を呼びました。 これが、SG法を用いた生産技術を確立し、量産化を目指す2006〜2010年度の「カーボンナノチューブキャパシタ開発プロジェクト」のベースとなりました。 図4 量産化を目指し日本ゼオンを訪れたときのことを語る湯村さん(左)と畠さん(右) 間を引き裂かれた恋人とようやく再会した思い 量産化を目指すには、企業との連携が欠かせません。そこで、湯村さんがパートナーとして白羽の矢を立てたのが、日本ゼオンでした。日本ゼオンにとって、カーボンナノチューブはこれまでまったく扱ったことがない材料です。それにもかかわらず、湯村さんはなぜ、日本ゼオンを選んだのでしょうか。 湯村さんはこう振り返ります。 「1998年、私は、NEDO『炭素系高機能材料技術の研究開発』のカーボンナノチューブの担当リーダーを務めていました。日本として、何とか生産技術を確立したいと考え、過去の研究論文や出願特許を調査していました。そのとき、荒川公平さんという人が非常に先駆的な研究をされていることを知り、お話を聞きたいと考えていました」 荒川さんは、1983年に「気相流動法」と呼ばれる多層カーボンナノチューブの連続製法を発明し、多くの特許を取得していました。「発明当時、カーボンナノチューブがもつポテンシャルの高さに魅了されたのを、今でも鮮明に覚えています」と荒川さんは語ります。 しかし、用途開発について荒川さんは当時いた会社と方針が合わずに転職、カーボンナノチューブとは別の分野の研究をすることになりました。その後、荒川さんは再度転職し、日本ゼオンで液晶ディスプレー用の光学フィルムの開発に携わることになります。しかし荒川さんにはカーボンナノチューブに強い未練があり、ずっと忘れることができなかったと言います。 「2005年5月に日本ゼオンで湯村さんにお会いし、カーボンナノチューブにかかわるNEDOプロジェクトへの参画のお誘いをいただいたときは、昔、引き裂かれた恋人との再会を果たした思いがしました」と荒川さん。 そして、「今度こそカーボンナノチューブを量産化し、応用製品を世に送り出したい」と、荒川さんは20年以上前に抱いていた熱い思いを呼び覚ましたのです。 立ちはだかる壁あるニュースから会社が量産化に二の足 カーボンナノチューブの生産技術の開発は、日本ゼオンにとってはまったくの新規事業です。しかし、日本ゼオンの社長は産総研の技術を信頼し、NEDOプロジェクトへの参画を快諾してくれました。 ところが、安堵したのも束の間。「アスベストショック」が荒川さんを襲います。これは、機械メーカーの兵庫県尼崎市にある旧工場で、周辺住民の多くに中皮腫などの健康被害が発生した事件です。2005年6月には、その原因としてアスベストの有害性が大きくクローズアップされることとなりました。それにともない、同じ繊維状の無機物ということから、カーボンナノチューブの身体への影響が危惧されるようになってしまいます。 「社長からは、『当社として、カーボンナノチューブの量産化に関与することはできないだろう』と告げられました。しかし、私も湯村さんもどうしてもあきらめることができませんでした」と荒川さん。 そこで、畠さんが研究開発を進めていた産総研のクリーンルームの空調機に装備されているヘパフィルターと呼ばれるエアフィルターに、カーボンナノチューブが含まれていないかどうかを調査するため、畠さんの研究チームは、電子顕微鏡を使って丹念に調べ上げました。その結果、ヘパフィルターには1本のカーボンナノチューブも含まれていないことを確認したのです。 その調査結果を基に、荒川さんは役員会議でNEDOプロジェクトへの参画を強く要望。納得した社長から「量産化は別にして、研究開発であればやってもよし」という方針を引き出したことで、2006年夏、「カーボンナノチューブキャパシタ開発プロジェクト」に参画することができました。 BREAKTHROUGH プロジェクトの突破口 産総研に送り込まれた成否を分ける技術をもった人材 日本ゼオンは産総研との共同研究開発を進めるに当たり、つくばにある産総研の研究所に2人の社員を常駐させることになりました。 しかし、日本ゼオンにはカーボンナノチューブの研究開発に携わった経験のある社員は1人もいません。また、日本ゼオンにとっては、荒川さんの強い意向で許可したプロジェクトです。荒川さんは自分の直属の部下から人選する以外ありませんでした。 「産総研にはカーボンナノチューブの専門家がたくさんいます。それに対し、私が送り込んだ部下が常に産総研の指示に従って行動しているようでは、足手まといになるだけ。それは絶対に避けたいと思いました。そこで、産総研に不足している人材を調査したところ、2点あると見えたのです。それは、ガスの熱流体シミュレーションが行える人材と、最適な触媒を開発できる人材です。そこで、熱流体シミュレーションのプロと触媒のプロの2人の部下を産総研に送り込むことにしました」と荒川さんは語ります。 この読みの背景にあったのが、事業化に至るまでのビジョンです。荒川さんと畠さんは、単層カーボンナノチューブを量産化するには、基板の“大面積化”と、合成装置の“連続運転”の2つがカギを握ると考えていました。 SG法では、基板の表面に触媒となる鉄の超微粒子をまんべんなく均一に付けた状態で、800°Cという高温の電気炉の中に入れます。そのうえで、電気炉の中にカーボンナノチューブの原料となるエチレンガスと鉄の触媒機能を助ける極微量の水蒸気を流し込みます。 このとき、電気炉の中のエチレンガスや水蒸気などの濃度を均一にする必要があります。そのためには、電気炉の中のガスの気流を制御することが不可欠です。実現するには、熱流体シミュレーションを扱える人材が必要です。 また、従来SG法では、基板の表面に鉄の超微粒子を「スパッタリング」と呼ばれる堆積法で付けていました。しかし、スパッタリングでは真空装置が必要なため、生産性が低く、高コストで量産化には向きません。 そこですでに畠さんが考えていたのが、ウェットコーティングでした。これは溶媒に触媒となる鉄の化合物を溶かし、それを基板の表面に塗布し、さらに乾燥させることで、鉄の超微粒子をコーティングするという方法です。そして、そのためには、大面積の基板に最適な大きさの触媒をまんべんなく均一に形成できる技術に精通した人材が必要だと読んだのです。 この2つの課題に挑戦できる人材として、荒川さんが選び出したのが、渋谷明慶さんと高井広和さんでした。 「渋谷くんは流体シミュレーションのプロで、当初、ワイヤグリッド偏光板(WGP)と呼ばれる部材の研究開発で、高い成果を出していました。しかし偏光板よりもカーボンナノチューブの方が、将来性が高いと考え、WGPの研究開発を無理矢理中断させ、産総研に行ってもらうことにしました」と荒川さん。 一方、高井さんは化学が専門です。当時、従事していた光学フィルムの研究開発では塗布型のものも開発していたので、その経験も生かせるだろうと考えました。 荒川さんの目論見は見事に的中しました。渋谷さんと高井さんは、プロジェクト開始直後から大きな成果を出し始めたのです。 基板を大面積化、さらに生産コストを1000分の1に まず、量産化するためには、当初4cm角だった基板を大面積化していく必要がありました。そこで渋谷さんは、A4サイズの基板を投入できる電気炉を設計しました。 当初、SG法では、電気炉の内部をクリーンにするためにヘリウムガスを使っていました。しかし、量産化には低コスト化が不可欠です。そのためには、ヘリウムガスからより安価な窒素ガスに切り替える必要がありました。とはいえ、ヘリウムガスと窒素ガスでは粘度が異なるため、電気炉に入れた際にガスの流れ方がかなり異なってきます。そこで、渋谷さんは熱流体シミュレーションを駆使し、電気炉の内部にガスを均一に流すための最適な条件を割り出しました。 一方、高井さんは、A4サイズの基板に触媒を付けるため、溶媒の配合や塗布の仕方を検討し、試行錯誤を重ねます。その結果、2人は、A4サイズの基板に単層カーボンナノチューブを結晶成長させることに見事成功しました。 続いて、連続運転のプロセス設計に取り組みました。 連続運転では、まず鉄の超微粒子を均一に付けた基板を、電気炉の中にベルトコンベアで挿入します。しかし、鉄の超微粒子は空気中の酸素とすぐに反応してしまいます。そこで、水素ガスを電気炉の中に投入し、鉄を還元します。そのため、電気炉の内部の温度を約800°Cという高温にしています。次に、エチレンガス、水蒸気を投入します。すると、基板上に単層カーボンナノチューブが成長し始めます。最後に、電気炉から出てきた基板上の単層カーボンナノチューブを回収します。加えて、連続運転をするため、単層カーボンナノチューブを回収したあとの基板は触媒をきれいに除去し、再利用します。 「使うガスは、窒素、エチレン、水蒸気、水素と4種類に及びます。それらの気流を最適に制御するためには、やはり熱流体シミュレーションが不可欠でした」と渋谷さん。 800°Cの水素ガスは、外に漏れたら爆発してしまいます。連続運転が可能な電気炉を設計するうえで最も配慮したことは、水素ガスを電気炉の中に確実に閉じ込めるということでした。 「水素が絶対に電気炉から漏れないようにしながら、連続的に基板が電気炉の中に入っていくように設計するのが大変でした」と渋谷さんは振り返ります。 加えて、電気炉は金属製を採用したことから、800°Cの高温になると金属の中に炭素原子が入り込む「浸炭」と呼ばれる現象が発生し、金属が大きく膨張することが判明しました。そのため、浸炭を考慮した設計を行う必要性も出てきました。 「製造を依頼した装置メーカーの方とは、約1年かけて、10回以上試行錯誤を繰り返しました。最初は、『こんな装置は作ったことがないので作れない』と言われたものです。しかし畠さんが粘り強くメーカーを説得してくれて、ようやく完成させることができました」(渋谷さん)。こうして2007年、9cm角の基板を使った連続運転が可能な電気炉の完成に成功しました〈図5〉。 図5 9cm角の単層カーボンナノチューブ 「連続運転が可能であると確認できたことにより、生産コストを従来の約1000分の1にできることもわかりました。プロジェクト期間中にこの装置開発まで達成できたことは、計画変更と加速資金が認められたことも非常に大きかったですね。その結果、自信をもって量産化を推し進めることができました」。畠さんはこう語ります。 FOR THE FUTURE 開発のいま、そして未来 量産化技術確立のためさらに人材を投入 2009年に日本ゼオンと産総研は、つくばイノベーションアリーナナノテクノロジー(TIA-nano)事業の1つとして経済産業省の補助を受け、つくばの産総研で量産実証プラントの開発に着手しました。 並行して2010年5月には、複数の企業を中心に、単層カーボンナノチューブなどのナノ炭素材料の実用化を目指して「技術研究組合単層CNT融合新材料研究開発機構(TASC)」が発足。日本ゼオンと産総研はその組合員としてオープンイノベーションによる単層カーボンナノチューブの実用化のための基盤技術の開発を進めました。 そのために2009年に新たに加わったのが、現在、日本ゼオン総合開発センターCNT研究所で所長を務める上島貢さんと、チームリーダーを務める廣田光仁さんです。上島さんは、量産実証プラント全体のマネジメントを担当、一方、廣田さんは高井さんとともに、基板のさらなる大面積化に取り組みました。量産実証プラントでは、50cm角という大きさの基板を用いることになったのです〈図6〉。 しかし、大面積化すると単層カーボンナノチューブの品質がどうしても低下してしまいます。 ウェットコーティングでは、溶媒が乾燥していく過程で、鉄のイオンが徐々に凝集していき、微粒子を形成しています。しかし凝集した微粒子が大きすぎると、単層カーボンナノチューブにならず、多層カーボンナノチューブになってしまいます。そのため、純度が高く、高品質の単層カーボンナノチューブを作るには、粒径の揃った鉄の超微粒子を基板の表面に均一に形成することが重要です。基板の面積が大きくなればなるほど、その難易度は高まります。 加えて、事業化のためには、従来使っていたシリコンの基板を、より安価な金属基板に切り替える必要もありました。基板が変われば、溶媒の配合や塗布の仕方も変わってきます。そのため、高井さんは試行錯誤を重ねながら、完成度を高めていきました。一方、廣田さんは、基板の再利用のための技術開発に取り組みました。 図6 ついに50cm角までの大面積化に成功した単層カーボンナノチューブ 図7 従来の合成法との比較従来のプロセスでは基板にシリコン、触媒形成方法としてスパッタリングが用いられた。それに比べニッケル合金基板、ウェットコーティングはコストが小さく、さらに回収後の基板は再利用することにした(提供:日本ゼオン) 実証プラントの成果を手にいよいよ量産工場の建設へ さらに、日本ゼオンと産総研は、2011年に完成した量産実証プラントで製造したカーボンナノチューブをサンプルとして企業に提供する一方、NEDO「低炭素社会を実現するナノ炭素材料実用化プロジェクト」で応用材料の開発を進めることにも取り組みました。 そのなかで、上島さんは、応用材料の研究機関や企業と産総研との間に入り、研究機関や企業の要望を産総研に伝える役割を担ったほか、プロジェクトで試作した複合材料の評価技術の開発を担当しました。 「例えば、単層カーボンナノチューブを1%混ぜるだけで、鉄よりも熱伝導性が高いゴムが得られたり、0.01%混ぜるだけで、非常に高い電気伝導性を示すゴムが得られたりしました。アルミニウムに混ぜたときには、通常のアルミニウムの約3倍の熱伝導性を確認することができました。このように、たくさんの成果が次々に上がってくるようになったのです」と荒川さんは語ります。 図8 当プロジェクトの成果左)実証プラントで大量合成できるようになったスーパーグロース法単層カーボンナノチューブ右)アルミとカーボンナノチューブの複合材。高い熱伝導率、高い放熱特性をもつ(提供:産総研) そうなると、技術研究組合に参画している企業からは、「日本ゼオンさん、量産化して供給してくれるのでしょうね」と念を押されるようになっていきました。こうした声に応え、2014年、荒川さんは日本ゼオンの取締役会議で、量産工場の設置を提案しました。それが認められ、日本ゼオンは、山口県にある同社の徳山工場の敷地内に量産工場を建設することになりました。 図9 日本ゼオンの徳山工場高い塔は合成ゴムなどに用いるブタジエンを抽出する施設(提供:日本ゼオン) 徳山工場は隣接する別の会社から、エチレンガスと水素ガスをパイプラインで導入できるという恵まれた立地条件にあります。輸送コストが低く抑えられることも、生産コストの低減に貢献しています〈図10〉。 量産工場の建設に当たり、最も苦労したのが安全性の議論でした。 「『ナノ粒子特性評価手法の研究開発』プロジェクトから、安全性に関しては細心の注意を払ってきました。安全性については、産総研のフェローで環境リスク学を専門とする中西準子さんが、『カーボンナノチューブが、1m3当たり0.03mg以下の濃度であれば、人体に影響はない』ということを早い段階から示してくれたことが非常に大きかった。そのおかげで、自信をもって量産工場の建設に着手することができました。これもNEDOプロジェクトならではのメリットです」と荒川さんは語ります。 2010年から現在に至る「低炭素社会を実現するナノ炭素材料実用化プロジェクト」でも、引き続き安全管理技術の確立に取り組み、「安全性試験手順書」や「作業環境計測手引き」、具体的なナノ材料に適用した安全性管理に関する事例集「ケーススタディ報告書」を公開しています〈図11〉。これらの報告書は、工場立地にかかわる自治体の環境審議会に参考資料として提出され、認可に貢献しました。 図10 港から通じる高圧ガスのパイプライン輸送コストが低減できる(提供:日本ゼオン) 図11 安全な生産のための手引き引き続き2010年から始まったNEDOプロジェクトで作成された「安全性データおよびTASC自主安全管理の紹介」など(提供:産総研) そして、2015年11月、日本ゼオンは世界で初めてSG法で得られる高品位な単層カーボンナノチューブの量産工場を完成させました。ついに量産化を開始したのです。 「量産工場では、工場内の気圧を外の気圧に比べて少し低く抑えているほか、生産ライン全体をクリーンルームにし、クリーンルーム内の塵の全量を1m3当たり0.03mg以下に保つことで、基準値を十分に満たすことに努めています。これは中西先生の基準です。 また、近隣住民の皆様にご説明するためのセミナーも開催し、単層カーボンナノチューブに関する安全性の考え方について、説明のみならず質疑等も通じて精一杯お話しさせていただきました。こうして、地域の皆様にもご理解いただいたうえで、工場の竣工と稼働を進めることができたと考えています。また、時代の最先端をいく新材料の生産拠点が徳山にできたということで、応援の声もいただくことができました」と荒川さん。 図12 徳山新工場の前でNEDOプロジェクトを振り返る荒川さん NEDOプロジェクトを振り返り、SG法の生みの親である畠さんも最後にこう語ってくれました。「目指すのは近い将来、私たちが開発したこの単層カーボンナノチューブが非常に身近なものになっていること。よく周囲に言うのが、私の母も単層カーボンナノチューブ製品を普通に使っているような世界です。その思いは荒川さんも一緒です。思いが一緒だったことが、NEDOプロジェクトにおける一番の成功要因ではないかと考えています。といっても単層カーボンナノチューブの事業としては、ようやくスタート地点に立った段階です。今後は単層カーボンナノチューブの普及と市場の創造に向け、さらに研究開発に尽力していきます」 開発者の横顔 カーボンナノチューブのポテンシャルの高さに魅せられた 1983年、「気相流動法」と呼ばれる多層カーボンナノチューブの連続製法を発明した荒川さん。そのとき、カーボンナノチューブのポテンシャルの高さに魅了されたものの、会社と方針が合わず、以来カーボンナノチューブとは無縁の研究者生活を送っていました。しかし、NEDOプロジェクトへの参画を機に、長年の夢を果たすことになります。現在は単層カーボンナノチューブなどを扱うゼオンナノテクノロジー株式会社の代表取締役社長を務めます。 「いくら素晴らしい研究ができたとしても、企業としては、実用化が果たせなければ意味がありません。その点、産総研の畠さんとは最初から思いが一緒でしたので、量産工場の竣工までたどり着くことができたと思っています。また、NEDOの方々が高く評価し、適切なタイミングで資金を援助してくださったことも非常に大きい。とはいえ、量産工場の稼働開始はマラソンで言えばスタート地点に立ったばかり。今後は、事業を1日も早く軌道に乗せると同時に、カーボンナノチューブを通して豊かで幸せな社会の実現を目指していきたいですね」 日本ゼオン株式会社 特別経営技監/ゼオンナノテクノロジー株式会社代表取締役社長荒川公平さん カーボンナノチューブの研究開発歴25年のベテラン 1990年頃からカーボンナノチューブの研究開発に携わっていた湯村さん。1991年に世界で初めてカーボンナノチューブを発見した飯島澄男さんを産総研に招へいし、さらに日本ゼオンの荒川さんをNEDOプロジェクトに参画させたキーパーソン。2010年度からの「低炭素社会を実現するナノ炭素材料実用化プロジェクト」のプロジェクトリーダーです。 「単層カーボンナノチューブが日本で発見されてから25年間。NEDOプロジェクトが開始してから19年間。ようやく、カーボンナノチューブの量産化と実用化が見えてきました。一連のNEDOプロジェクトがなければ、目標の達成は難しかったでしょう。とはいえ、研究開発の手を緩めたら、とたんに世界に追いつかれてしまいますので、油断は大敵です。日本ゼオンの量産工場が軌道に乗ったら、私は次世代にバトンタッチしようと思っていますが、NEDOプロジェクトを通して、充実した研究生活を送ることができたことに感謝しています」 国立研究開発法人産業技術総合研究所ナノチューブ実用化研究センター 首席研究員/技術研究組合単層CNT融合新材料研究開発機構 CNT事業本部長湯村守雄さん スーパーグロース法(SG法)の開発者 物理工学が専門の畠さん。留学先のハーバード大学で、CVD法によるカーボンナノチューブの合成法を勉強したのをきっかけに、SG法の開発を思いつきました。 「3回にわたるNEDOプロジェクトでは、思う存分に研究をさせていただきました。そのおかげで、単層カーボンナノチューブの量産工場の稼働にまで発展させることができたと思っています。2004年にSG法を編み出したときは、まだ5mm角の非常に小さな基板でした。そのとき、当初計画よりも進捗が順調と認められ、世界の強豪から一層リードするために、NEDOが柔軟な計画変更と加速資金追加のマネジメントをしたことが、非常に大きかったですね。1日も早く、我々が開発した単層カーボンナノチューブが身近な存在になっている社会を実現させたいですね」 国立研究開発法人産業技術総合研究所ナノチューブ実用化研究センター センター長畠 賢治さん 熱流体シミュレーションで装置の大型化に貢献 コンピューターによる熱流体シミュレーションを通して、装置の大型化に寄与してきた渋谷さん。NEDOプロジェクトに参画する前は実際の装置開発をしたことがなく、非常に貴重な経験になったといいます。 「コンピューター・シミュレーションが専門だったため、NEDOプロジェクトで装置の開発に携われたことは、本当に貴重な経験になりました。技術者としての幅を広げることができ、抜擢してくれた荒川さんと、技術を惜しみなく私に伝授してくれた産総研の方々に大変感謝しています。今後はその恩返しとして、SG法を超えるカーボンナノチューブの合成法を開発して、カーボンナノチューブの普及に貢献したいと思っています」 日本ゼオン株式会社総合開発センターCNT研究所渋谷明慶さん 触媒の形成技術で基板の大面積化を実現 基板に触媒をまんべんなく均一に付けるという触媒形成技術で、基板の大面積化に大きな貢献を果たした高井さん。単層カーボンナノチューブの品質を左右する重要なプロセスを担当しました。 「NEDOプロジェクトでは、約9年間にわたり、朝から晩まで産総研で研究開発に没頭し、本当に充実した日々を送ることができました。30代の時期に、産総研の方々と活発な議論を交わしながら、技術を磨いていけたことは、私の一生の財産です。最初は本当に小さな基板から始まりました。これが徐々に面積を大きくしていく過程は、そのたびに感慨深いものがありました。これも、NEDOプロジェクトならではの醍醐味でしょう。今後も、NEDOプロジェクトでの経験を生かし、社会に役立つ製品の研究開発にまい進していきたいと思います」 日本ゼオン株式会社総合開発センターCNT研究所高井広和さん 量産化に向けて、評価技術の開発や安全性の保証を担当 廣田さんとともに2009年からNEDOプロジェクトに参画し、量産化に向けて、マネジメントを担当した上島さん。研究機関や企業の要望を産総研に伝えたり、できた複合材料の評価技術を開発したりしました。 「実を言うと、事業化に向けては、まず日本ゼオンの役員や社員にカーボンナノチューブの安全性を理解していただくことが最も大変な仕事でした。2010年からの『低炭素社会を実現するナノ炭素材料実用化プロジェクト』で安全管理の手引きを作成してくれたため、これが社内外の説得に役立ちました。これに合わせて新しい成果も出てきたため、社内の反応も大きく変わり始め、応援モードになっていきました。今後は、是非とも単層カーボンナノチューブの量産工場を軌道に乗せたいと思っています」 日本ゼオン株式会社総合開発センターCNT研究所 所長上島 貢さん 量産化に向けて基板の再利用化に尽力 量産実証プラントの開発に当たり、高井さんのサポートとして2009年に上島さんとともにNEDOプロジェクトに参画した廣田さん。大面積化した基板を再利用するため、基板の回収・洗浄装置などの開発を担当しました。 「日本ゼオンでは、コンピューター・シミュレーションを行っていました。NEDOプロジェクトでは、実証プラントの設計、開発に携わることができ、貴重な経験となりました。最も印象に残っているのが、2011年3月11日の東日本大震災です。私はそのときは産総研にはいなかったのですが、つくばでもさまざまな被害が報告されていました。私は、まっさきに量産実証プラントのことが気になり、問い合わせたところ、まったく問題ないとの回答。図らずも、安全設計が立証された形となりました。今後も、量産工場の安全操業に向け、尽力していきたいと思います」 日本ゼオン株式会社総合開発センター CNT研究所 チームリーダー廣田光仁さん なるほど基礎知識 応用製品と将来社会 NEDOでは、単層カーボンナノチューブ等のナノ炭素材料について、多くの企業での実用化研究を加速させるために、「ナノ炭素材料応用製品技術ロードマップ」を作成しました。ナノ炭素材料が将来どのような応用製品で利用されるのか、また、利用されるためにはどのような仕様のナノ炭素材料を開発する必要があるのかを示しています。 図13 2030年の社会におけるナノ炭素材料の波及イメージ(屋外編) 図14 2030年の社会におけるナノ炭素材料の波及イメージ図(屋内編) 図14 2030年の社会におけるナノ炭素材料の波及イメージ図(屋内編) 図14 2030年の社会におけるナノ炭素材料の波及イメージ図(屋内編) NEDOの役割 「カーボンナノチューブキャパシタ開発プロジェクト」 (NEDO内担当部署:材料・ナノテクノロジー部) NEDOは1998年から2016年まで、19年間にわたって単層CNT等のナノ炭素材料実用化のためのプロジェクトを実施。新素材の基礎から応用までを複合的に進めるために、世界の情勢や研究開発動向を踏まえ、産学官の多様なプレイヤーの連携を支援するプロジェクトマネジメントを推進しました 1.柔軟なプロジェクト遂行世界をリードするため、当初計画を前倒した予算執行や加速予算追加、新テーマ立案を実施しました。例えば、安全管理技術開発へのニーズの高まりに対応するため、実施内容を拡充。また、CNTの他にも有望とされる新素材「グラフェン」の研究開発を新たに追加し、加速器センサーの製品化にも成功しました。 2.戦略的な知財ルールでサンプル提供と実用化を促進産学官の連携拠点でつくり出したサンプルをプロジェクト外部企業に提供するに当たり、プロジェクト外部企業各社の実用化を後押しし、かつ、産学官連携の研究活動も妨げないようなサンプル提供の知財ルールを設計しました。その結果、100件を超えるサンプル提供が行われ、多数の製品化に向けた研究開発の支援につながり、量産化の実現を後押ししました。 関連プロジェクト 「炭素系高機能材料技術の研究開発」(1998〜2001年度) 「ナノカーボン応用製品創製プロジェクト」(2002〜2005年度) 「カーボンナノチューブキャパシタ開発プロジェクト」(2006〜2010年度) 「低炭素社会を実現するナノ炭素材料実用化プロジェクト」(2010〜2016年度) お読みいただきありがとうございました。ぜひともアンケートにお答えいただき、お読みいただいた感想をお聞かせください。いただいた感想は、今後の連載の参考とさせていただきます。 アンケートに回答する (法人番号 2020005008480) NEDO WebMagazineとは サイト利用について ©New Energy and Industrial Technology Development Organization. All rights reserved. Top -->
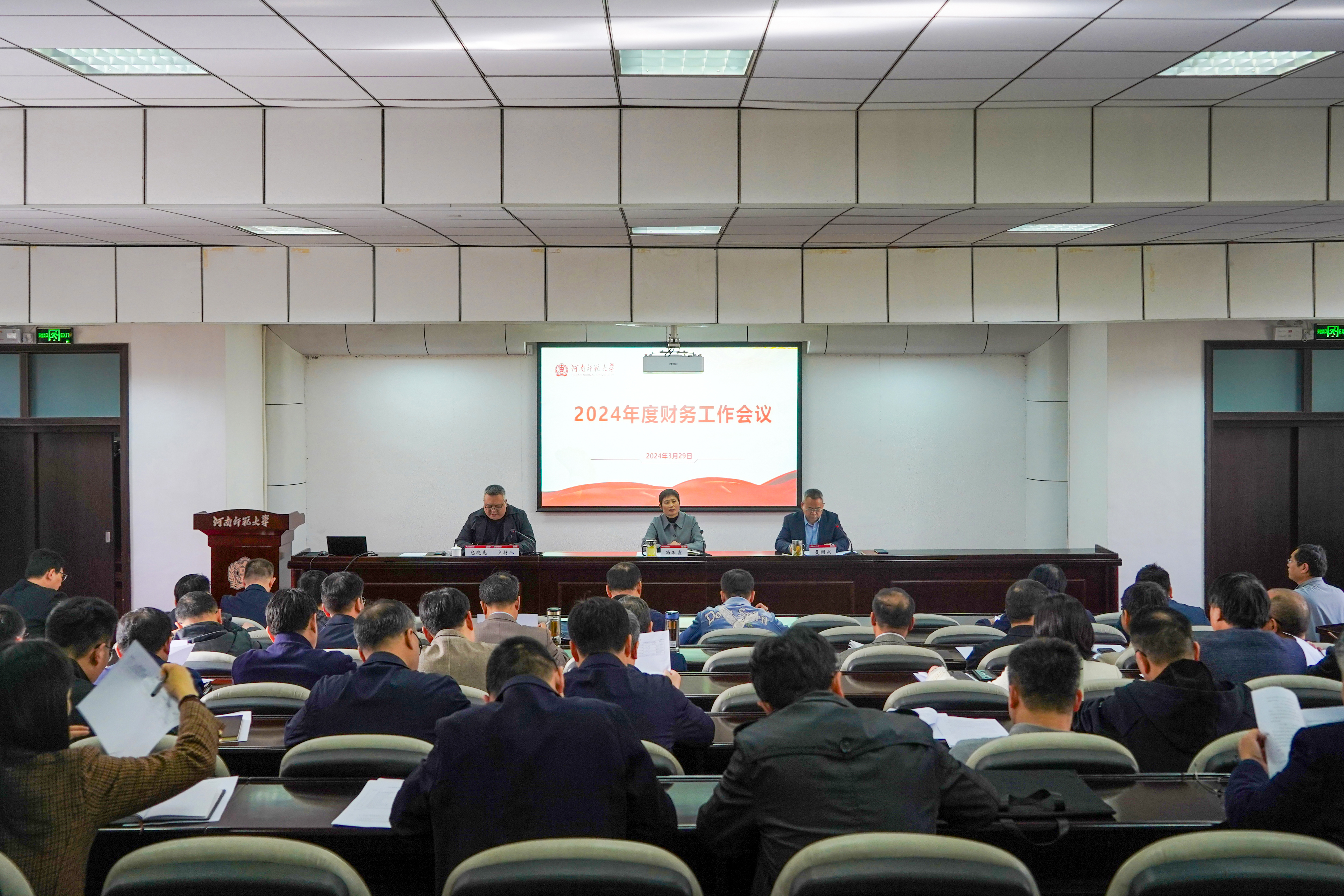