<ウェブサイト名>
<現在の時刻>
About KSC 日本語 Intelligent Gas Supplying SystemRealizing smart factories that harnesses cutting-edge technology Feb. 1, 2023 / TEXT BY YUYA OYAMADA / ILLUSTRAIONS BY SHINJI HAMANA※ Article updated on Dec. 1, 2021 Semiconductors have become an indispensable part of our daily lives. The related production process uses various kinds of industrial gases. At conventional semiconductor factories, workers engage in hard physical work, replacing gas cylinders each weighing over 100 kilograms dozens of times a day. Moreover,daily maintenance and inspections are required under law at work sites that use high-pressure gas, including semiconductor factories. This is tremendously time-consuming and labor-intensive work for production sites that are facing labor shortages. In response, Taiyo Nippon Sanso Corporation, a group company of the Mitsubishi Chemical Group (the MCG Group), developed the Intelligent Gas Supplying System (IGSS). IGSS brings digital innovation to the gas industry, providing support for converting gas supplying sites into smart factories. The company launched the system in July 2020. Taiyo Nippon Sanso Corporation commenced development of IGSS in 2017. This was when the concept of a “smart factory,” which emerged in the Fourth Industrial Revolution aimed at saving energy and manpower in manufacturing with digital technologies, was attracting attention in Japan. A smart factory is defined as being able to continuously reform processes, and improve quality and productivity by incorporating cutting-edge technologies, such as AI and IoT, into a full range of tasks at the manufacturing site. Why do semiconductor factories, which triggered the development of IGSS, need to turn into smart factories? This is because gas supplying sites face a number of challenges. Indeed, semiconductor factories are already automated and unmanned in most of their operations. In this sense, they already have turned into smart factories. However, there are still some manual tasks, such as replacing gas cylinders, maintenance, and inspections. In addition, such manufacturing sites are facing labor shortages. Taiyo Nippon Sanso Corporation, a company that has built partner relationships with semiconductor and other electronics factories as a supplier of industrial gasses, aimed to resolve the challenges its customers face through digital innovation that leads to realizing smart factories. The company defined the project concept as: “Provide ease to make our customers’ business more KAITEKI* by providing them with the concept of KAITEKI gas equipment.” It set a development goal to automate a full range of gas supplying operations by leveraging the latest technologies, such as robots, AI, sensors, and cloud services. * KAITEKI is an original concept of the Mitsubishi Chemical Group. The Group uses the word kaiteki to encapsulate the idea of the well-being of people and the planet. In this project, fast-paced actions were also required to keep up with the rapidly advancing digital technologies. The project members at Taiyo Nippon Sanso Corporation are experts with handling gas, but have little knowledge about technologies, including IoT and AI. Thus, the company promoted open innovation with other corporations that have the expertise, and adopted a methodology called “agile development,” in which a project progresses with repeated trial and verification processes in a short period of time. In the conventional development methodology, a requirements definition is clarified from the very start and processes are implemented step by step toward completion. However, with agile development methodology, a product gradually takes shape in the course of development activities. Necessary functions and other requirements are defined by repeating the process from planning, designing, implementing, and verifying, in a short period of time and making a number of prototypes. This results in improving product quality within a short period. However, to improve the accuracy of trials and verifications, projects always need to be implemented in partnership with the customers who ultimately use the systems. If the collaboration is not close enough, repeated trials end in vain and consume costs and time. If this happens, the advantages of agile development cannot be fully utilized. In this regard, Taiyo Nippon Sanso Corporation was able to make maximum use of the methodology because it has offices (gas centers) located next to customers’ factory sites and has engaged in operations related to gas supply over many years. Based on the trust it has built with its customers, the company was able to perform detailed adjustments and improvements that reflected end users’ opinions by positioning itself as their joint partner on the project, while reporting and sharing information on the progress of the development and challenges in a timely manner. Developed through the above-mentioned efforts, IGSS is equipped with the seven following functions. Integrated with advanced technologies, this support system can resolve the challenges faced by gas supplying sites via digital technology. These seven services can be used separately in accordance with the customer’s needs. IGSS is expected to contribute to transforming the business model involving gas supplying operations. The manufacturing business has been shifting toward a type of service business along with the expansion of the IoT, and widespread use of IGSS will help to create a new business that supports improving the efficiency of a variety of operations, in addition to supplying gas. A function like the labor-saving system for daily inspections is applicable to not only the gas supplying business, but also in a wide array of fields. In particular, as the MCG Group has diverse businesses, Taiyo Nippon Sanso Corporation hopes to collect ideas for a wide range of applications. However, IGSS is not fully completed yet. Just as the automation level of self-driving cars has increased gradually along with the progress of technology, the level of IGSS can be further raised from the current state. The company will continue incorporating the latest technology into IGSS and advancing the system to pursue an ideal smart factory. Digital innovation started in the gas industry, where there are many tasks requiring a human workforce. Next, this innovation could realize a smart factory in the future. IGSS serves as the initial step toward this dream. Share Back to Index Share Recommended Implantable Engineering Plastics Performance Materials and Technical Support Power Advancements in Artificial Joints Carbon Fiber & Composites Aiming to create a resource efficient future with “light weight and strong materials” Precision Medicine Creating hope for all facing illness Terms of Use Privacy Policy Copyright © Mitsubishi Chemical Group Corporation. All Rights Reserved. TOP About KSC 日本語 Terms of Use Privacy Policy
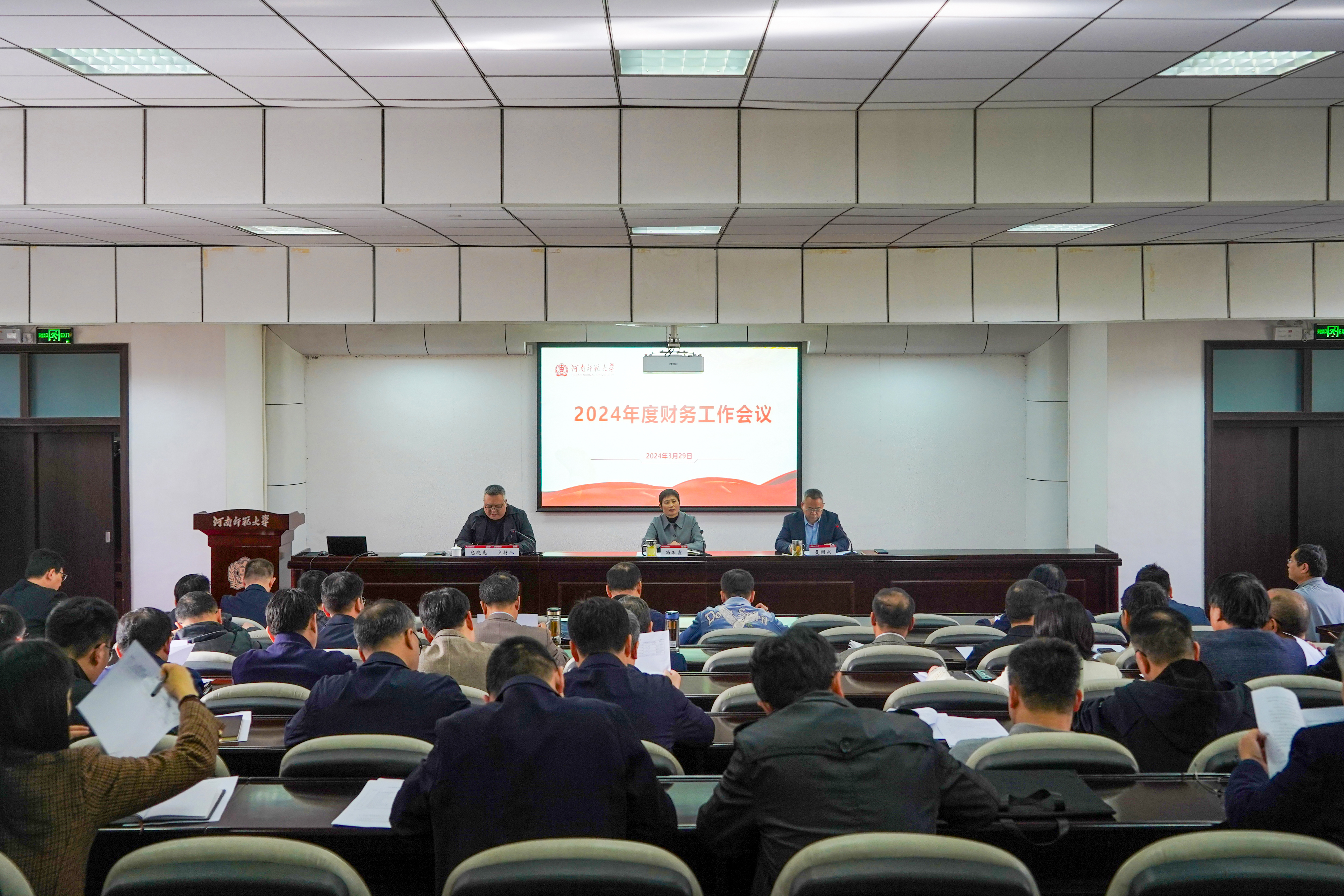